Berta Sándor
Radarral elemezhető az üvegszálas termékek gyártása
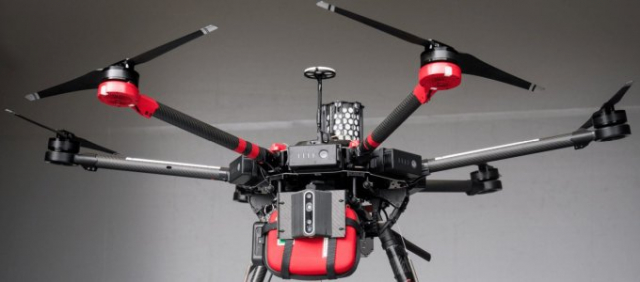
A jövőben lehetséges lesz a szálkompozit anyagok hibáinak felismerése már a gyártási folyamat során egy új radaros módszer segítségével, amely lehetővé teszi az érintett anyagok roncsolásmentes és automatikus ellenőrzését. Eddig a szakemberek ezt kézzel, vizuális ellenőrzéssel végezték.
Az üvegszál-erősítésű szerkezeti elemek gyártása során - mint például a rotorlapátokban - a szálszerkezetet gyantamátrixszal rögzítik. A szálerősítés igazításának vagy menetének a szabálytalanságai megváltoztatják a szerkezeti tulajdonságokat és így csökkentik a kapott kompozit anyag minőségét. "A rotorlapátok gyártása során üvegszálak rétegeit fektetik egymásra egy héjban. Amennyiben ezt nem pontosan végzik el, különböző hibák, például hullámképződés léphet fel. De a szálak iránya is elfordulhat, és így befolyásolhatja az alkatrész mechanikai tulajdonságait" - magyarázta Dr. André Froehly, a Fraunhofer Társaság projektvezetője.
Eddig nem lehetett megbízhatóan vizsgálni a szálak irányát és a szálak rétegződését a gyantamátrix felhordása előtt, így a hibás helyeket csak utólag, például ultrahangos vizsgálattal lehetett megtalálni. Ez lehetetlenné tette az ellenőrzött folyamatláncot és az alkatrészek költségigényes átdolgozásához vagy akár selejtezéséhez vezetett. Ezért fejlesztett ki a Fraunhofer Társaság, a Bochumi Ruhr Egyetem, az Aacheni Alkalmazott Tudományok Egyeteme és az Aeroconcept GmbH munkatársai közösen egy innovatív radaros módszert.
A FiberRadar projektben megalkotott egység egy robotból, egy polarimetrikus radarból és a hozzá tartozó képalkotó szoftverből álló milliméterhullámú pásztázó rendszerből áll. A megoldás az elektromágneses hullámok polarizációját (az antennatechnikában használt kifejezés, amely az elektromágneses hullámok elektromos térkomponensének irányát jelöli) is felhasználja, ami azt jelenti, hogy a polarizáció irányának megváltoztatásával az esetleges hibákat is felismeri. A robot letapogatja az alkatrészt, a radar elvégzi a méréseket, amelyeket a szoftver 3D-képpé állít össze.
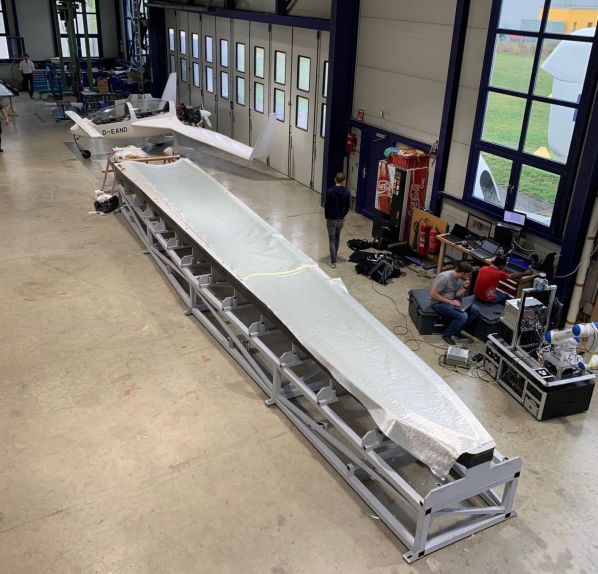
A repülőgépek szárnyaiban a legkisebb anyaghiba sem engedhető meg
Az eljárás különlegessége, hogy amíg a hagyományos radarok csak egy csatornával rendelkeznek és így egy polarizációt használnak az adáshoz és a vételhez, az új radar két polarizációban küldi a jeleket és két polarizációban is fogadja azokat. Ez nem csupán a szálszerkezetek nagy felbontású leképezését teszi lehetővé, hanem a mélyebb rétegekben lévő hibák feltárását is megkönnyíti. Emellett a fénytörés-kompenzáció javítja a képminőséget: kiküszöböli a fénytörésből adódó, különösen a mélyebb rétegekben problémás hatásokat. Az egyes rétegek radarral történő leképezésével a kutatók a szálak orientációjában mutatkozó eltéréseket is felismerhetik és roncsolásmentesen ellenőrizhetik az anyag teljes térfogatát.
A FiberRadar projektben a Ruhr Egyetem integrált radartechnológiáját, a Fraunhofer Intézet algoritmus-szakértelmét és az Aacheni Alkalmazott Tudományok Egyeteme robotikai kompetenciáját használták fel egy olyan mérőrendszer megvalósításához, amely lehetővé teszi a szálkompozitok gyártását és a gyártott alkatrészek eddig elérhetetlen pontosságú ellenőrzését. Az Aeroconcept GmbH tapasztalatainak köszönhetően a technológia így közvetlenül integrálható a gyártás és az ellenőrzés folyamatába a szélturbinalapátok gyártása területén, és a kiváló minőségű kompozit anyagok kulcsfontosságú technológiája megalapozható.
"Nagyon elégedettek vagyunk a FiberRadar végén elért ígéretes eredményekkel. Tervezzük, hogy a rendszert a termékérettség felé továbbfejlesztjük a követő projektek során, hogy a gyártási folyamatban is felhasználhassuk. Itt nem csupán a sebességet, hanem a mélységi felbontást is javítani szeretnénk, hogy még több lehetséges hibát tudjunk rövidebb idő alatt felismerni" - nyilatkozta Froehly a következő lépésekről. A projektet az Európai Regionális Fejlesztési Alap (ERFA) finanszírozta.
Az üvegszál-erősítésű szerkezeti elemek gyártása során - mint például a rotorlapátokban - a szálszerkezetet gyantamátrixszal rögzítik. A szálerősítés igazításának vagy menetének a szabálytalanságai megváltoztatják a szerkezeti tulajdonságokat és így csökkentik a kapott kompozit anyag minőségét. "A rotorlapátok gyártása során üvegszálak rétegeit fektetik egymásra egy héjban. Amennyiben ezt nem pontosan végzik el, különböző hibák, például hullámképződés léphet fel. De a szálak iránya is elfordulhat, és így befolyásolhatja az alkatrész mechanikai tulajdonságait" - magyarázta Dr. André Froehly, a Fraunhofer Társaság projektvezetője.
Eddig nem lehetett megbízhatóan vizsgálni a szálak irányát és a szálak rétegződését a gyantamátrix felhordása előtt, így a hibás helyeket csak utólag, például ultrahangos vizsgálattal lehetett megtalálni. Ez lehetetlenné tette az ellenőrzött folyamatláncot és az alkatrészek költségigényes átdolgozásához vagy akár selejtezéséhez vezetett. Ezért fejlesztett ki a Fraunhofer Társaság, a Bochumi Ruhr Egyetem, az Aacheni Alkalmazott Tudományok Egyeteme és az Aeroconcept GmbH munkatársai közösen egy innovatív radaros módszert.
A FiberRadar projektben megalkotott egység egy robotból, egy polarimetrikus radarból és a hozzá tartozó képalkotó szoftverből álló milliméterhullámú pásztázó rendszerből áll. A megoldás az elektromágneses hullámok polarizációját (az antennatechnikában használt kifejezés, amely az elektromágneses hullámok elektromos térkomponensének irányát jelöli) is felhasználja, ami azt jelenti, hogy a polarizáció irányának megváltoztatásával az esetleges hibákat is felismeri. A robot letapogatja az alkatrészt, a radar elvégzi a méréseket, amelyeket a szoftver 3D-képpé állít össze.
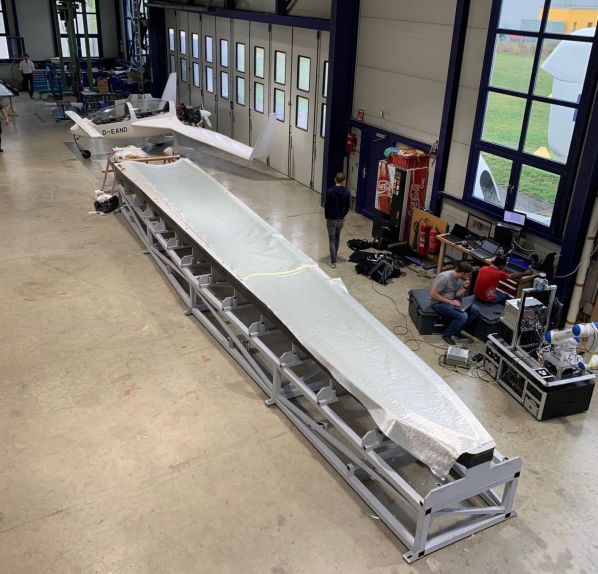
A repülőgépek szárnyaiban a legkisebb anyaghiba sem engedhető meg
Az eljárás különlegessége, hogy amíg a hagyományos radarok csak egy csatornával rendelkeznek és így egy polarizációt használnak az adáshoz és a vételhez, az új radar két polarizációban küldi a jeleket és két polarizációban is fogadja azokat. Ez nem csupán a szálszerkezetek nagy felbontású leképezését teszi lehetővé, hanem a mélyebb rétegekben lévő hibák feltárását is megkönnyíti. Emellett a fénytörés-kompenzáció javítja a képminőséget: kiküszöböli a fénytörésből adódó, különösen a mélyebb rétegekben problémás hatásokat. Az egyes rétegek radarral történő leképezésével a kutatók a szálak orientációjában mutatkozó eltéréseket is felismerhetik és roncsolásmentesen ellenőrizhetik az anyag teljes térfogatát.
A FiberRadar projektben a Ruhr Egyetem integrált radartechnológiáját, a Fraunhofer Intézet algoritmus-szakértelmét és az Aacheni Alkalmazott Tudományok Egyeteme robotikai kompetenciáját használták fel egy olyan mérőrendszer megvalósításához, amely lehetővé teszi a szálkompozitok gyártását és a gyártott alkatrészek eddig elérhetetlen pontosságú ellenőrzését. Az Aeroconcept GmbH tapasztalatainak köszönhetően a technológia így közvetlenül integrálható a gyártás és az ellenőrzés folyamatába a szélturbinalapátok gyártása területén, és a kiváló minőségű kompozit anyagok kulcsfontosságú technológiája megalapozható.
"Nagyon elégedettek vagyunk a FiberRadar végén elért ígéretes eredményekkel. Tervezzük, hogy a rendszert a termékérettség felé továbbfejlesztjük a követő projektek során, hogy a gyártási folyamatban is felhasználhassuk. Itt nem csupán a sebességet, hanem a mélységi felbontást is javítani szeretnénk, hogy még több lehetséges hibát tudjunk rövidebb idő alatt felismerni" - nyilatkozta Froehly a következő lépésekről. A projektet az Európai Regionális Fejlesztési Alap (ERFA) finanszírozta.